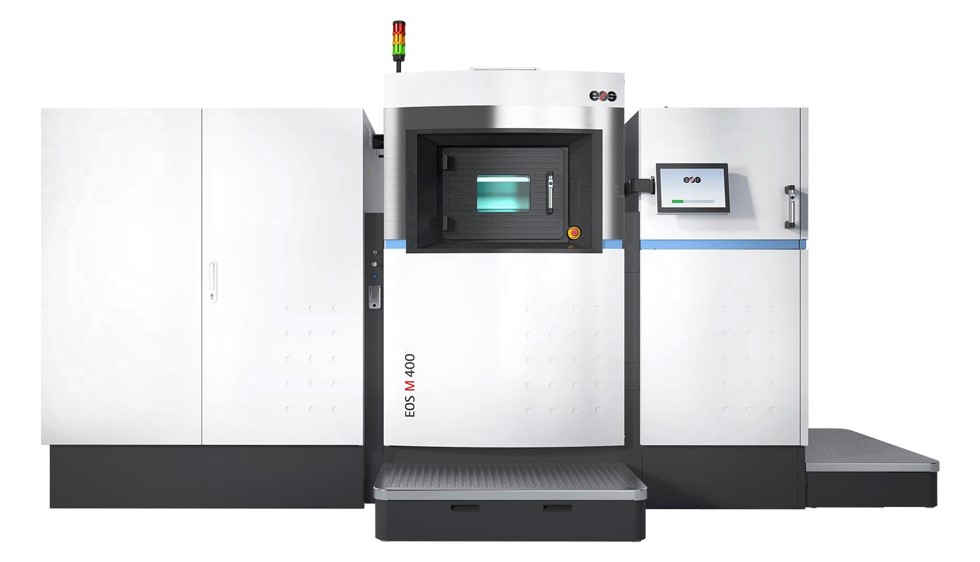
For centuries, CNC machining has dominated the way we produce metal components for the die casting and plastic injection industries. CNC manufacturing in combination with other machining operations offers a reliable process chain to bring metal stocks into the desired form. Therefore, companies have accepted the resulting months-long lead time until start of production and adapted to the limitations of CNC manufacturing by design flexibility, design complexity, rigid production planning schedules, which limits the overall design and manufacturing freedoms.
3D Printing (or Additive Manufacturing) technologies promised to offer what tooling engineers were looking for: a digital process chain with high freedom of design, cnc-less manufacturing with lead times of days instead of months, small carbon footprint, reduced waste and the potential for optimized lightweight structures. Possibilities appeared endless and provided engineers with a seemingly inexhaustible toolbox, waiting to be discovered. Additive Manufacturing seemed to be the holy grail of modern manufacturing and allowed for completely new part designs.
AarKel Tool & Die Inc. has confidently invested in Metal 3D Printing Technology. A new additive manufacturing lab has been constructed at the main plant 1 facility in Wallaceburg, Ontario, Canada. Our additive manufacturing team is set to begin research and development leading to innovation and key breakthroughs in the tooling industry. Unlocking advanced cooling solutions to manufacturing complex part geometries and much more!
We are very excited in acquiring an EOSM400-1 metal 3d printing machine. This huge investment in 3D printing will help AarKel design, manufacture and innovate in our complex tooling world.